From Raw Materials to Advanced EV Batteries: A European Success Story
The push for electric vehicles (EVs) is driving significant innovation in battery technology. A major EU project, spearheaded by Empa, has concluded after four years with impressive results focused on improving EV batteries. The project, known as SeNSE, involved eleven collaborators from both research institutions and industry, and was designed to accelerate the development of the next generation of lithium-ion batteries, focusing on sustainability, safety, and energy density.
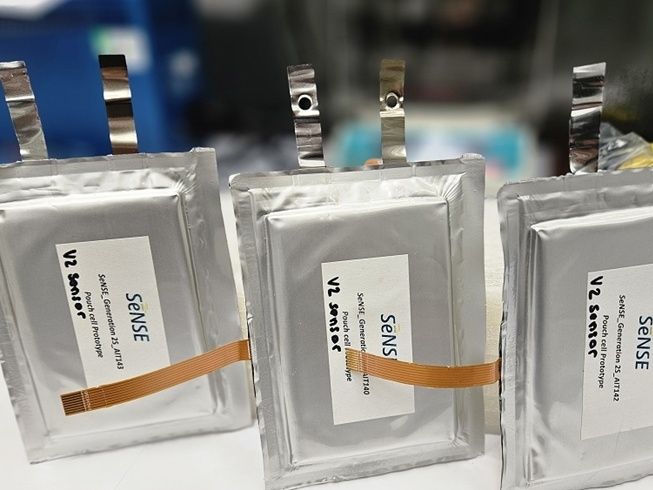
SeNSE Consortium
The Drive for Better Batteries
With the impending ban on the sale of new combustion engine cars in Europe after 2035, the need for enhanced battery technology is paramount. The SeNSE project directly addressed this challenge by aiming to create batteries that charge faster, offer greater driving range, and have a reduced environmental footprint. Corsin Battaglia, the head of Empa’s Materials for Energy Conversion laboratory, emphasized the project’s dual objectives: practical advancements with a focus on the “next” generation rather than the one after that, with a goal of bringing the technology to market within a few years.
“We are also researching battery technologies that are potentially worlds better than lithium-ion batteries – more sustainable, safer and with a higher energy density,” Battaglia noted. “But it will still be a few years before they can be produced industrially. In SeNSE, we wanted to develop technologies that can be installed in market-ready electric cars within a few years.”
Advancements Across the Battery Value Chain
The SeNSE project showcased the complete production value chain in a short four-year timeframe. It covered everything from new material development to the production of complete battery cells. The Austrian Institute of Technology (AIT) manufactured the pouch cells, similar in size to a smartphone, while FPT Motorenforschung AG, part of the Iveco Group’s Innovation center, integrated these cells into ready-to-use modules suitable for electric vehicles.
Key Improvements and Innovations
The SeNSE module boasts several improvements compared to existing batteries. These include:
- Higher energy density: Delivering more power in a smaller space.
- Improved environmental balance: Using more sustainable materials.
- Fast-charging capabilities: Reducing charging times.
- Increased fire safety: Minimizing risks associated with thermal events; and,
- Cost-effectiveness: Making the technology commercially viable.
All core components received focused improvements during the project. The cathode now utilizes half as much of the critical raw material cobalt compared to today’s batteries. The anode incorporates silicon to replace some of the graphite which is also classified as a critical material. Empa researchers also spearheaded improvements to the electrolyte, the liquid which conducts ions between the electrodes enabling charging and discharging. “Conventional electrolytes are flammable,” explained Empa researcher Kühnel. “We were able to greatly reduce the flammability by using certain additives without impairing the conductivity, which is key for fast charging and discharging.”
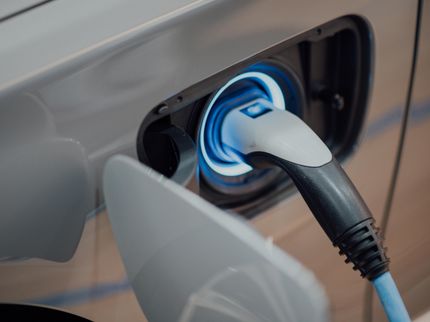
Machine learning algorithm predicts how to get the most out of electric vehicle batteries
To further enhance the fast-charging capabilities, Coventry University and FPT Motorenforschung AG collaborated on the development of an advanced thermal management system incorporating sensors inside the battery cells to monitor temperatures in real time. A custom algorithm then controls the charging rate, preventing overheating. Battaglia and Kühnel celebrate both the scalability of the project and the direct transfer of the technology developments to industrial partners. The involved industrial teams have already secured multiple patents and financing for pilot plants and further battery technologies.
Overcoming Hurdles and Looking Ahead
The SeNSE project, despite its successes, encountered challenges including pandemic-related organizational and logistical issues, unstable supply chains, and rising material costs. Furthermore, the project team hopes to improve stability in the prototype cells. Also, while successful, the scaling process presented its own challenges. Battaglia explained, “We have scaled up all new developments from laboratory to pilot scale. For production in a so-called gigafactory, of, e.g., project partner Northvolt, producing multiple gigawatt hours of batteries per year, the entire material production process would have to be scaled up once more, say, by a factor of 1000.”
While SeNSE concludes, the Empa researchers are already focusing on the next European battery project. Additionally, they have established a joint cluster for battery research with its sister projects and regularly exchange ideas and share results. The coordinators plan to launch IntelLiGent, a collaborative Horizon Europe research project focused on developing cobalt-free high-voltage cells for electric cars.