New Forms of Steel for Stronger, Lighter Cars
Every pound saved in a car’s weight matters, whether it’s about reducing fuel consumption in gasoline-powered cars or extending the driving range of electric vehicles.
Like many other useful innovations, the creation of high-quality steel by Indian metallurgists thousands of years ago appears to have been a confluence of skillful craftsmanship and sheer luck. Firing lumps of iron with charcoal in a specialized clay container produced something entirely new, which the Indians called wootz. Soon, Roman armies were wielding wootz steel swords to terrify and subdue the wild, hairy tribes of ancient Europe.
Twenty-four centuries later, automakers are utilizing electric arc furnaces, hot stamping machines, and quenching and partitioning processes—techniques that the ancients could never have imagined. These methods are yielding innovative strategies to refine steel, protecting human bodies during inevitable crashes and simultaneously reducing car weights to minimize their detrimental impact on the planet.
“It is a revolution,” says Alan Taub, University of Michigan engineering professor with extensive experience in the industry. The new steels, numbering in the dozens of varieties and continuously expanding, when combined with lightweight polymers and carbon fiber-spun interiors and underbodies, hark back to the heady days at the start of the last century when, he says, “Detroit was Silicon Valley.”
Such materials can cut the vehicle’s weight by hundreds of pounds, and every pound saved on excess weight saves roughly $3 in fuel expenses over the car’s lifespan, making the economics undeniable. The new approach, according to Taub, is to use “the right material in the right place.”
The Importance of Materials in the Age of EVs
The transition to battery-powered vehicles highlights the importance of these new materials. Electric vehicles may not emit pollution, but they are heavy. For instance, the Volvo XC40 Recharge is 33 percent heavier than its gasoline counterpart – and would be even heavier if the steel cage surrounding occupants was as bulky as it once was.
Heavy can be dangerous.
“Safety, especially when it comes to new transportation policies and new technologies, cannot be overlooked,” Jennifer Homendy, chief of the National Transportation Safety Board, told the Transportation Research Board in 2023. Moreover, reducing the weight of an electric vehicle by 10 percent brings a roughly 14 percent enhancement in range.
As recently as the 1960s, the steel cage surrounding passengers was made using what automakers call soft steel. This outdated armor from Detroit’s Jurassic period was not very different from what Henry Ford had implemented decades before. It was dense, and there was a great deal of it.
With the 1965 publication of Ralph Nader’s Unsafe at Any Speed: The Designed-In Dangers of the American Automobile, major automakers realized they could no longer focus solely on speed and performance. The oil embargos of the 1970s further accelerated this shift: Automotive steel now needed to be both stronger and lighter, requiring less fuel to move about.
Modern Advances in Steel Manufacturing
In response, over the past 60 years, steelmakers — their arc furnaces reaching thousands of degrees Fahrenheit, with robots doing much of the work – have created a wide variety of steels to fulfill every need. There are high-strength, hardened steels for chassis components, stainless steels that resist corrosion for side panels and roofs, and highly stretchable metals in bumpers to absorb impact without crumpling.
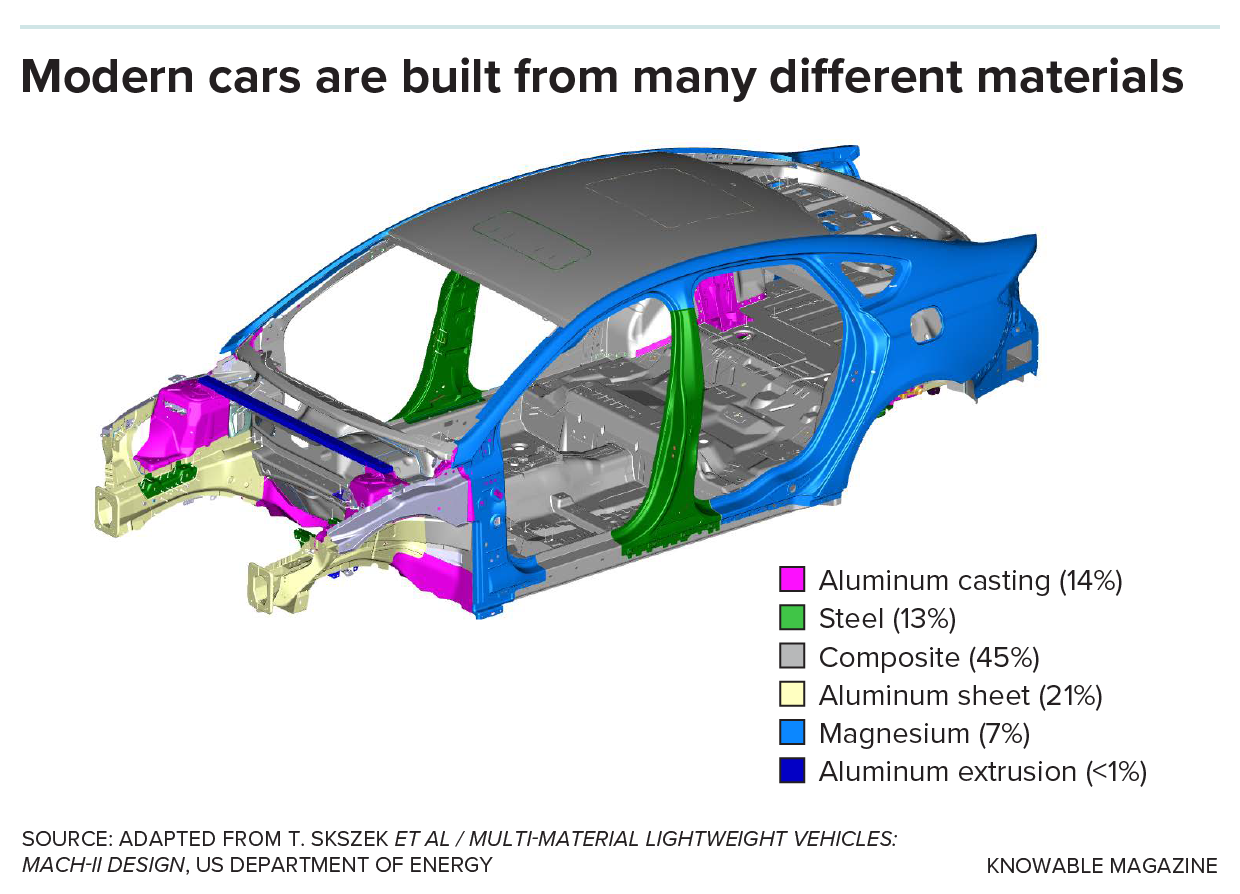
Carmakers use a wide range of materials to build a car’s body, choosing the material that works best for each application.
Most steel is composed of more than 98 percent iron. The remaining couple of percent – sometimes only hundredths of a single percent, in the case of metals added to provide desired properties – makes the difference. Equally vital are treatment methods, including heating, cooling, and processing steps such as rolling the sheets before forming parts. Modifying each of these factors, sometimes by mere seconds, changes the metal’s structure to yield different properties.
“It’s all about playing tricks with the steel,” says John Speer, director of the Advanced Steel Processing and Products Research Center at the Colorado School of Mines.
At the most basic level, the properties of steel relate to its microstructure: the arrangement of different types, or phases, of steel within the metal. Certain phases increase hardness while others confer ductility. This ductility measure indicates how much the metal can bend and twist out of shape without shearing and creating sharp edges that penetrate and tear human bodies. At an atomic scale, there are principally four phases found in automotive steel, including the very hard yet brittle martensite, and the more ductile austenite. Automakers can alter these by adjusting the times and temperatures of the heating process to produce the properties they want.
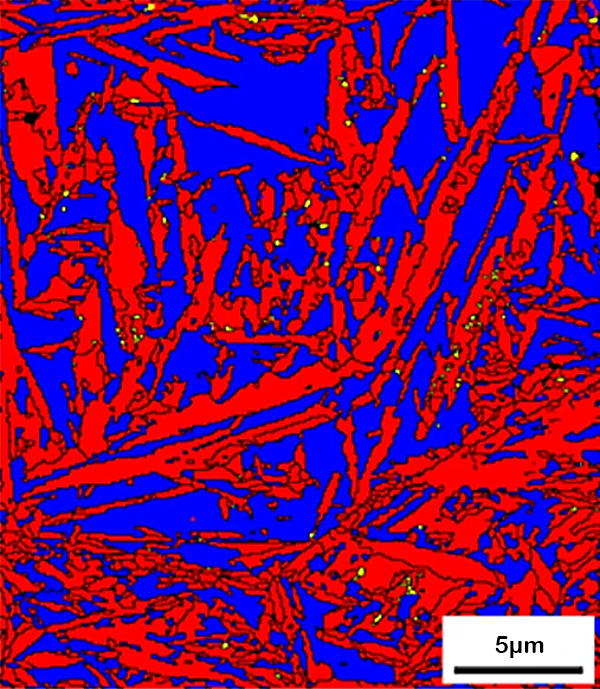
Academic researchers and steelmakers, in strong partnership with automakers, have advanced three generations of what is now called advanced high-strength steel. The first generation, adopted in the 1990s and still broadly in use, offered a good blend of strength and ductility. A second generation used more exotic alloys to achieve even greater ductility, however, these steels proved both expensive and difficult to manufacture.
The third generation, which Speer states is beginning to appear on the factory floor, uses heating and cooling methods to generate steels that are both stronger and more formable than the first generation, almost ten times as strong as common steels of the past, and much less costly (although less ductile) than the second-generation steels.
Steelmakers have found that the cooling time is a crucial factor in developing the final atomic arrangements and, hence, the steel’s properties. The most rapid cooling, known as quenching, freezes and stabilizes the internal structure before further changes can occur during the hours or days it would otherwise take to reach room temperature.
One of the strongest types of modern auto steel, used in the most critical structural components such as side panels and pillars, is made by superheating the metal with boron and manganese to temperatures exceeding 850 degrees Celsius. After becoming malleable, the steel transfers within ten seconds to a die, or form, where the part is shaped and rapidly cooled.
Advanced Techniques and Alloys
In one version of what’s referred to as transformation-induced plasticity, the steel is heated to a high temperature, cooled to a lower temperature, held there for a period, and then rapidly quenched. This creates islands of austenite surrounded by a matrix of softer ferrite, with regions of harder bainite and martensite. This specialized steel can absorb a large amount of energy without fracturing, making it useful in bumpers and pillars.
Recipes can be further tweaked using various alloys. Henry Ford was employing steel and vanadium alloys more than a century ago to improve the performance of steel in his Model T, and alloy recipes continue to improve today.
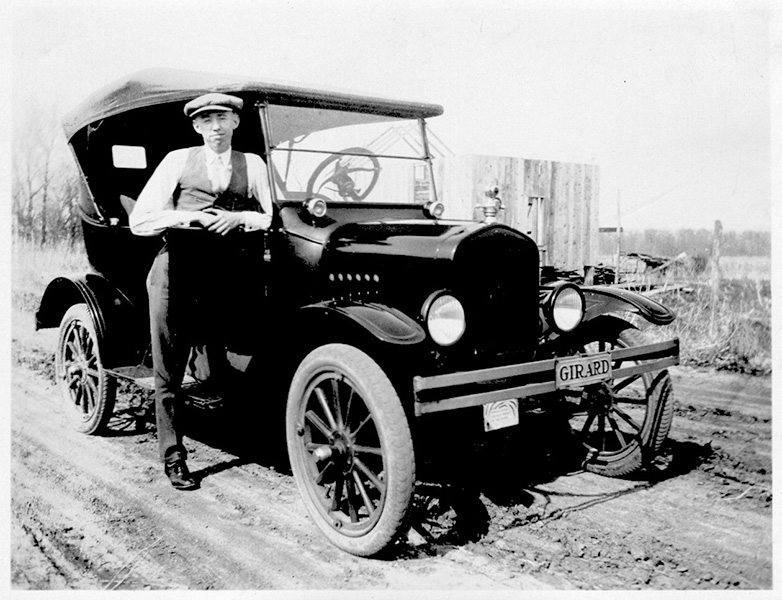
One modern example of using lighter metals in combination with steel is the Ford Motor Company’s aluminum-intensive F-150 truck, where the 2015 version weighs nearly 700 pounds less than the model that came before it. Another process used in conjunction with new materials is tube hydroforming, where a metal is bent into complex shapes by injecting high-pressure water or another fluid into a tube, effectively expanding it into the shape of a surrounding die. This technique allows parts to be made without having to weld the two halves together. This saves time and money.
A Corvette aluminum frame rail, the largest hydroformed part in the world, saved 20 percent in mass compared to the equivalent steel rail it replaced, according to Taub, who coauthored a 2019 article on automotive lightweighting in the Annual Review of Materials Research.
More recent introductions are alloys that utilize titanium and especially niobium, which enhance strength by stabilizing the metal’s microstructure. In a 2022 paper, Speer called the introduction of niobium “one of the most important physical metallurgy developments of the 20th century.”
One tool now shortening the distance between trial and error is the computer. “The idea is to use the computer to develop materials faster than through experimentation,” says Speer. New concepts can now be assessed down to the atomic level without the need for workers bending over a workbench or firing up a furnace.
The ongoing quest for improved materials and methods prompted engineer Raymond Boeman and his associates in 2015 to found the Institute for Advanced Composites Manufacturing Innovation (IACMI), supported by a $70 million federal grant. Commonly referred to as the Composites Institute, it serves as a hub where the industry can originate, assess, and upscale new processes and products.
“The field is evolving in a lot of ways,” says Boeman, who now directs the institute’s research on upscaling those processes. IACMI has been researching climate-friendly alternatives for conventional plastics like polypropylene. In 1960, less than 100 pounds of plastic were integrated into the typical vehicle. By 2017, this figure had risen to nearly 350 pounds, because plastic is inexpensive to manufacture and has a high strength-to-weight ratio, making it perfectly suited for automakers trying to cut down weight.
By 2019, according to Taub, 10-15 percent of a typical vehicle consisted of polymers and composites, spanning from seat components to trunks, door parts, and dashboards. And when those vehicles reach the end of their operational lives, this unrecyclable plastic and other materials known as automotive shredder residue, around 5 million tons in total, ends up in landfills — or, even worse, in the broader environment.
Clearly, more work is needed to make cars less of a threat both to human bodies and to the planet where those bodies perform their daily tasks. But Taub is optimistic about the future of Detroit and the industry’s capacity to address the challenges that have emerged since the transition from horse-and-buggy days. “I tell students they will have job security for a long time.”